Arsenic-containing non-fired process ores and concentrates in recovering gold from refractory bacterial leaching
At present, foreign countries by underground leaching and heap leaching from lean ore, ore and waste rock outside the balance sheet beneficiation plant tailings and mining enterprises in the leaching of copper and uranium, has been successfully using bacterial leaching method.
We are now studying how to treat concentrates of non-ferrous metals and precious metals by tank bacterial leaching in order to recover valuable components or remove impurities.
Studies using microbial leaching of refractory arsenic-containing concentrates have shown that sulphur leaching rates can be increased by hundreds of times under optimal conditions such as pH , slurry temperature, particle size of the original concentrate, oxygen and carbon dioxide, and ore concentration.
The trough bacterial leaching method is different from the underground leaching method and the heap leaching method, and has many unique features. Leaching is carried out in large tanks or Pachuca tanks. Therefore, bacteria are oxidized much faster in these devices than in subsurface leaching and heap leaching. Leaching is carried out in concentrated pulp, so the bacterial leaching method is suitable for treating concentrates having a much higher sulphide content than ore or waste rock.
Since the trough bacterial leaching method has the above characteristics, its leaching efficiency depends on a variety of special factors. A large amount of different elemental ions are accumulated in the leachate, for example, the arsenic content is up to
The results of studying the interaction between microorganisms and mineral particles using an electron microscope and a manometer show that the microorganism (T. thermophilus) can be firmly fixed to the mineral surface after 10 to 15 minutes of contact during the leaching process . Other bacteria present in the slurry phase can only participate indirectly in the leaching process and allow the ferric sulphate to be regenerated.
In addition to conducting theoretical studies on a laboratory scale, several processes have been developed to deal with difficult gold - arsenic concentrates. These gold - arsenic concentrates are characterized by varying amounts of gold, arsenic, carbon, antimony and other elements.
Several processes are included direct bacterial leaching, after leaching the solution purification of the bacteria, the bacteria solution is returned to use and the like leached I cyanation step. For a period of two or bacterial leaching Pachuca tank in air with stirring. The leaching conditions are as follows: solid: liquid = 1 : 5 , concentrate particle size is 90~95%-0.074 mm, pulp temperature is 28~
After leaching for 60~120 hours, the oxidation rate of the arsenopyrite can reach 80~90% . The leaching residue after bacterial leaching is subjected to cyanidation of the elbow, and the gold recovery rate can reach 86 to 91% . However, if the concentrate is cyanated directly without pre-leaching by bacteria, the gold recovery rate is only 10 to 32% .
The high arsenic - gold concentrate processing process (see Figure 1 ) consists of two stages of bacterial leaching. After the leaching of the I stage bacteria, the slurry is classified according to the 40 micron size to separate the qualified products suitable for cyanidation. The yield is 25~30% of the original ore. After the leaching of the II stage bacteria, the product is leached. The arsenic content is reduced from 9-10% of the original concentrate to 1.3~1.4% . At this time, the recovery rate of arsenic sulfide is 89 to 91% . When the leaching residue is cyanated, the gold recovery rate is 90 to 91% , but the gold- carbon gold - arsenic concentrate which is not leached by the bacteria is very difficult to handle. Gold is symbiotic with poisonous sand in these concentrates. Danby concentrate contained gold - with a very high adsorption activity cyanide complex.
Metals, alloys and composite powders commonly used in thermal spray hardfacing technology and coating service. These unique powders are instantly heated by thermal spraying (welding) methods such as high temperature flame or explosive flame, and are sprayed and deposited on the cold or hot workpiece surface with high-speed heat flow in a molten or semi-melted state to form a surface Reinforcing layer, in order to improve the wear resistance, corrosion resistance, heat resistance, oxidation resistance or repair of external dimensions of the workpiece surface. XTC produces WC, CrC, Oxide Ceramic, Boride Powder, Metal Alloy Powder, Pure Metal and Spray Wire, etc. product. For HVOF/HVAF/plasma/Flame spray coating and applications. Meet the wear and corrosion resistance requirements of different surfaces.
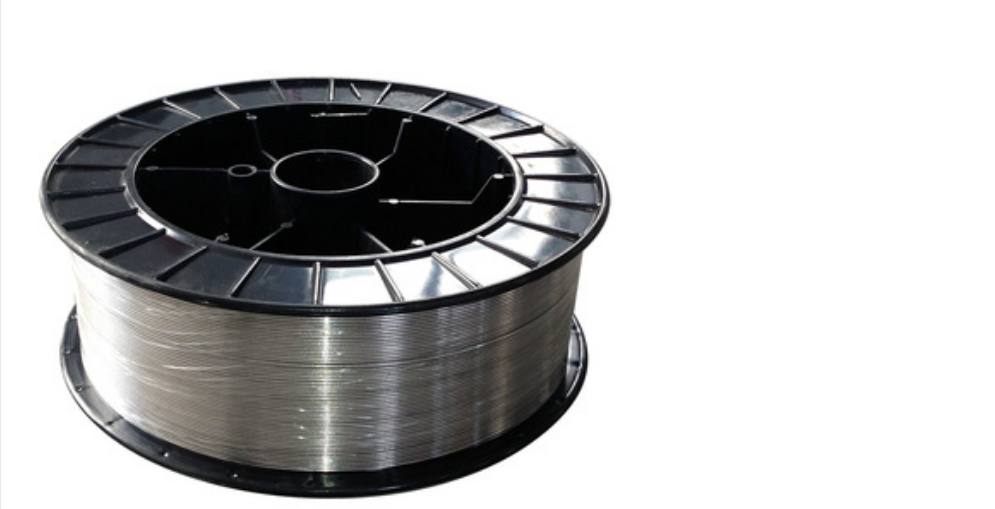
WC, CrC oxide ceramic powder and boride products are excellent in wear resistance and high temperature corrosion resistance. Taking WC products as an example, the hardness can reach HV1300-1500, and the temperature of CrC products can reach 800 degrees Celsius.
Metal alloy powder, Pure Metal and Spray Wire products have more applications in glass mold, steel and machinery industries. And XTC products are now become more and more popular in Metal spray coating and thermal spray coating industry.
Coating Service,Metal Spray Coating,Flame Spray Coating,Thermal Spray Coating
Luoyang Golden Egret Geotools Co., Ltd , https://www.lygoldentool.com