Two Stage Plastic Granulating Machine for PE Film and Bottle Scraps
The pellets produced by the recycling machine can be put directly back into the production line, in most cases for blown film or pipe extrusion processes.
1. Pellets from in-house, post-industrial recycling
On average, post-industrial waste makes up 5% or more of the entire production line, making in-house recycling very important nowadays as it can significantly reduce the cost of raw/virgin material purchasing.
The plastic pellets produced from in-house waste are almost like-new and can be re-used for producing high quality plastic products once again.
2. Pellets from post-consumer recycling
The ML two stage plastic recycling granulator is also designed to work with washed, post-consumer and used agricultural film. The cutter compactor, which generates frictional heat during the compacting process, helps to further dry and remove the water moisture from the washed film flakes (processed first by the washing lines). The recycled pellets can be used again in extrusion process, whether 100% (such as garbage bag, LDPE pipe production and etc) or as part of the mixture to reduce raw material cost. The pellets quality can also be improved by direct dosing of masterbatch and additives.
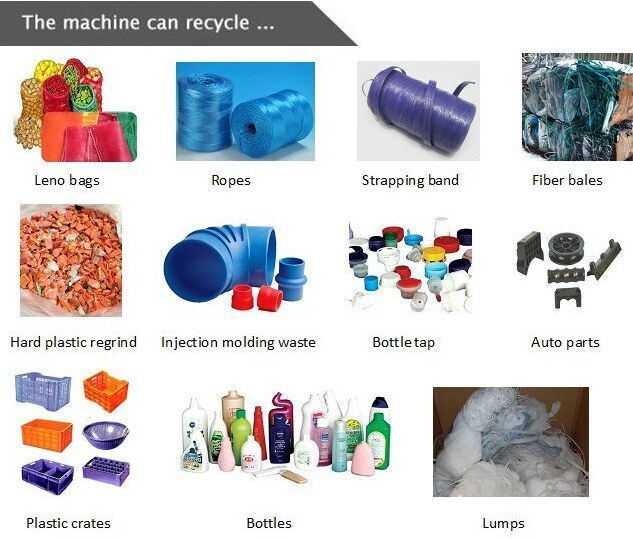
Parameters
PRODUCTS | PP/HDPE/LDPE/LLDPE/EVA/ABS/PS | |
MAX. OUTPUT /Â HR . | PP | 600KG |
HDPE | 700KG | |
LDPE | 800KG | |
INSTALLED POWER | 420KW | |
SHREDDING UNIT | DRIVING MOTOR | 110KW |
SHREDDER DRUM DIA(m/m) | 1300 | |
SHREDDING KNIVES | 9 FOR ROTARY | |
13 FOR STATIONARY | ||
EXTRUDER | SCREW DIAMETER(m/m) | Ø160mm |
L/D RATIO | 30/1 | |
SCREW RPM | 10-120 | |
BARREL HEATER | 75KW | |
BARREL COOLING | BY AIR | |
TEMPERATURE CONTROL ZONE | 0.5KW×5 |
Detailed photos
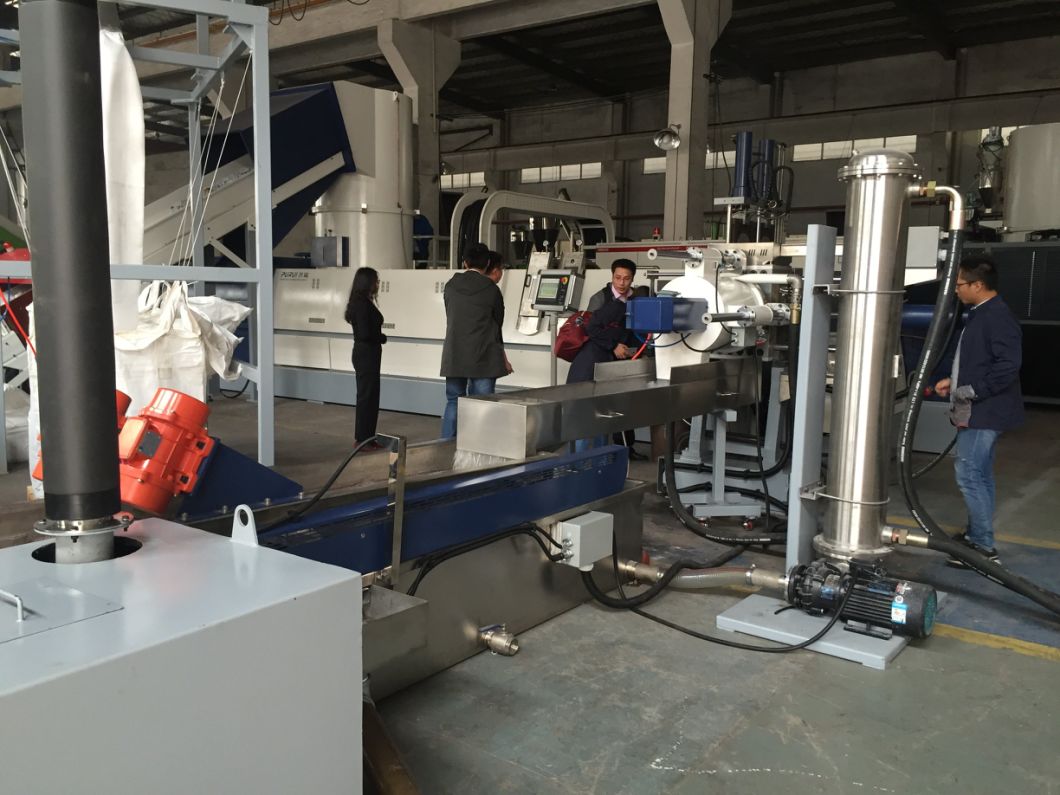
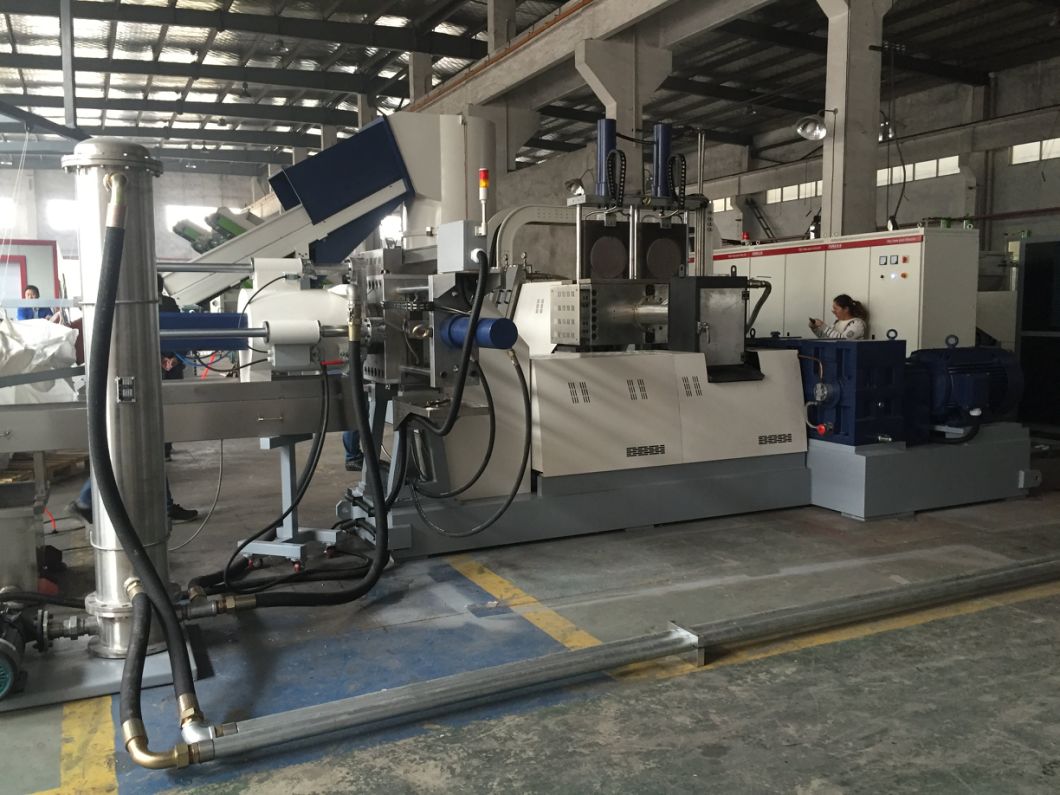
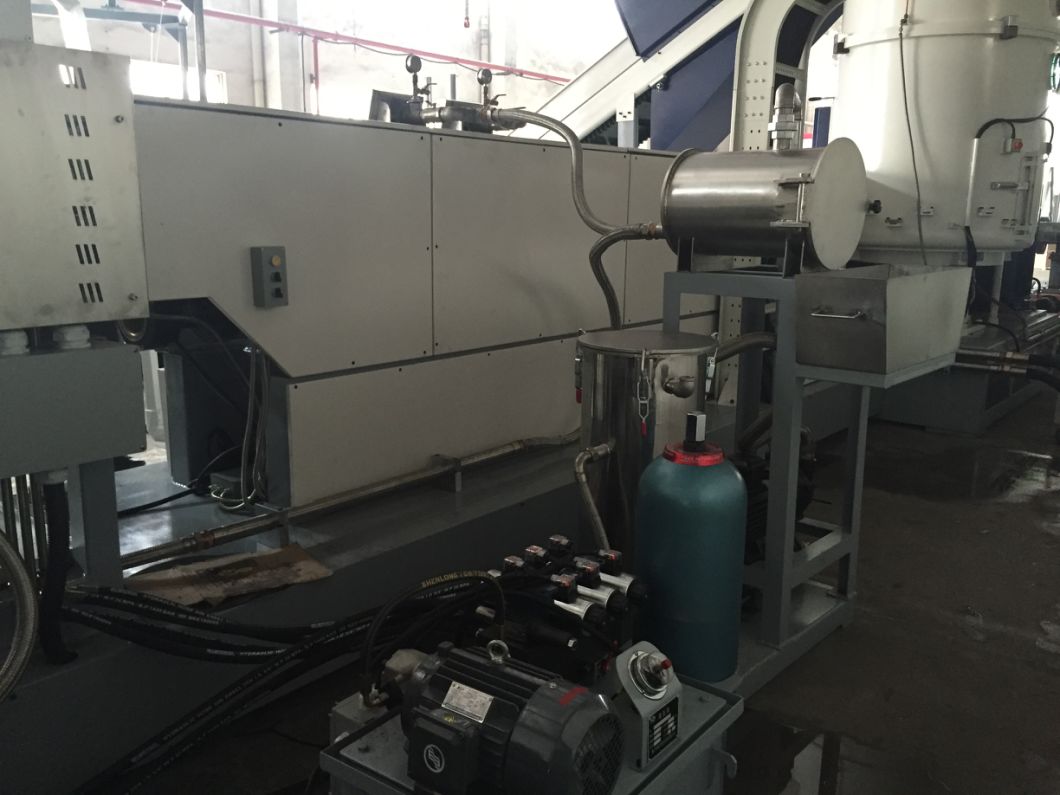
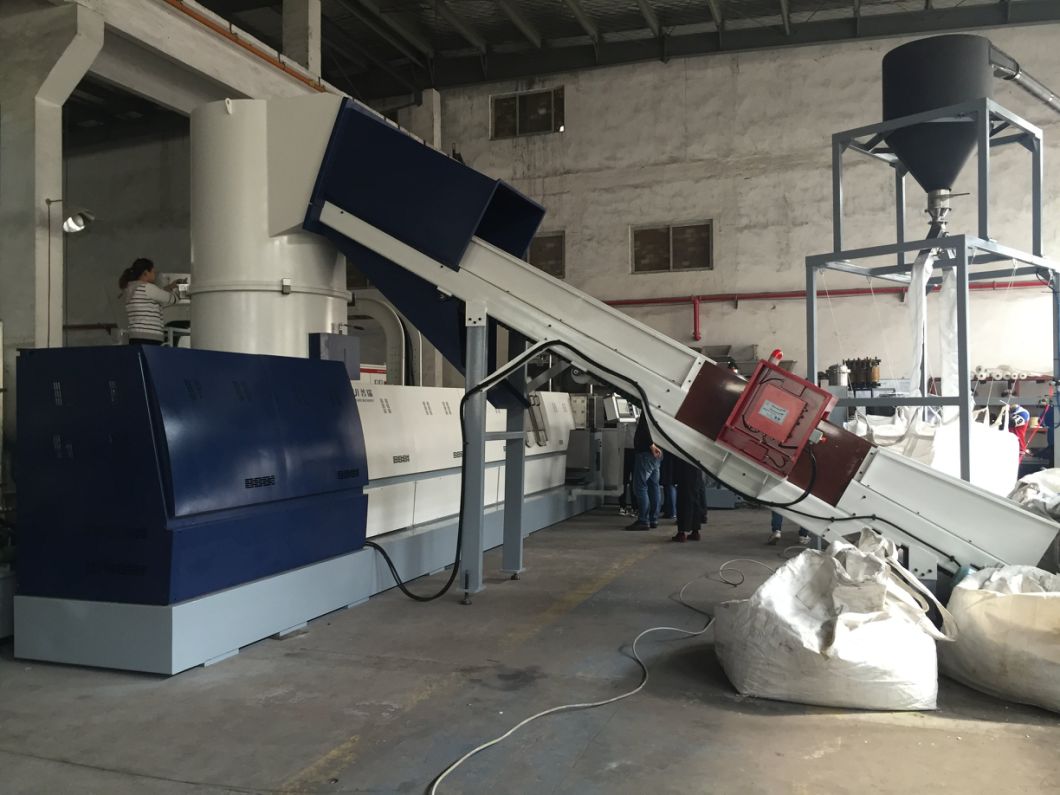
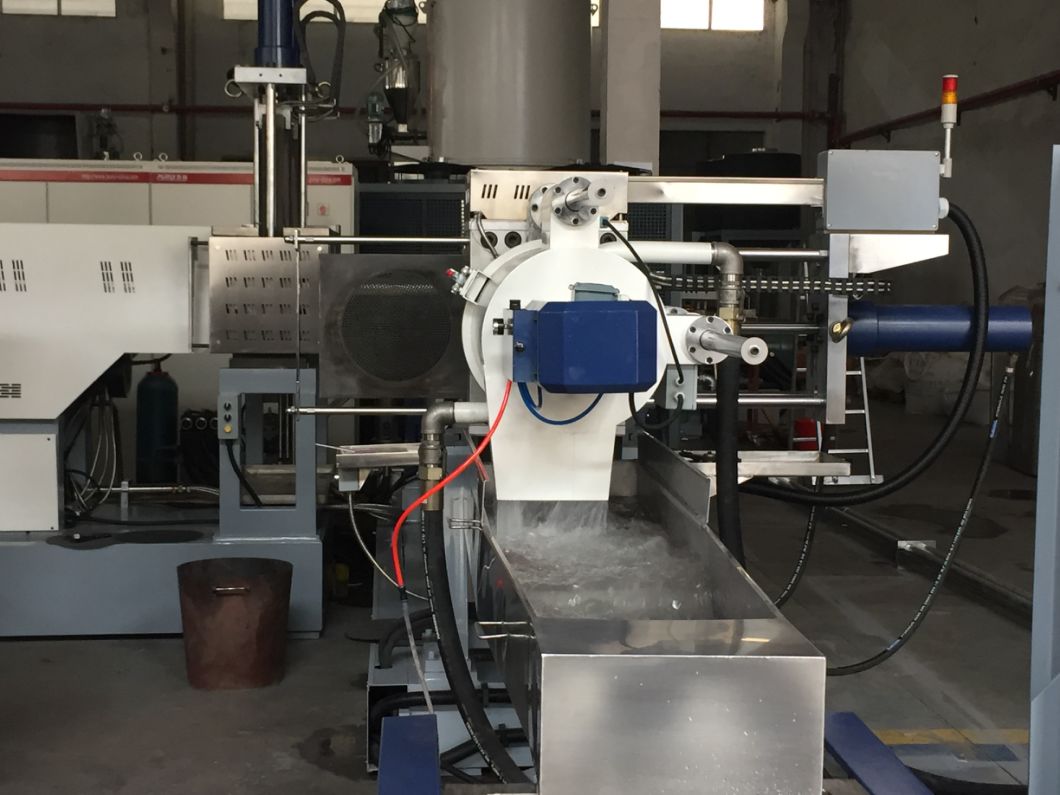
Before-sale
• Introduce products in detail  Â
• Recommend suitable solution  Â
• Offer test
During manufacturing
• Provide layout and engineering conditions  Â
• Offer screw plan and related documents
• Inform the project processing status Â
• Insure the product designed in accordance with technical document
After-sales service
• Send engineers to install, test the machines and offer technology guidance and worker training at customers' factory.
• Offer 12 months free maintenance and life long service. After the warranty period, spare parts will be provided at basic cost.
• Build customers database. All machines are traceable.
• Visit customers and make quality trace periodically and take customers' feedback into account during routine practices.
• Speed up service and spare parts supply.
Feel free to contact with me if you have any questions:
Contactor: Ms Laura
Mobile: 86 159 6236 6319Â : )
Two Stage Plastic Granulating Machine for PE Film and Bottle Scraps
The pellets produced by the recycling machine can be put directly back into the production line, in most cases for blown film or pipe extrusion processes.
1. Pellets from in-house, post-industrial recycling
On average, post-industrial waste makes up 5% or more of the entire production line, making in-house recycling very important nowadays as it can significantly reduce the cost of raw/virgin material purchasing.
The plastic pellets produced from in-house waste are almost like-new and can be re-used for producing high quality plastic products once again.
2. Pellets from post-consumer recycling
The ML two stage plastic recycling granulator is also designed to work with washed, post-consumer and used agricultural film. The cutter compactor, which generates frictional heat during the compacting process, helps to further dry and remove the water moisture from the washed film flakes (processed first by the washing lines). The recycled pellets can be used again in extrusion process, whether 100% (such as garbage bag, LDPE pipe production and etc) or as part of the mixture to reduce raw material cost. The pellets quality can also be improved by direct dosing of masterbatch and additives.
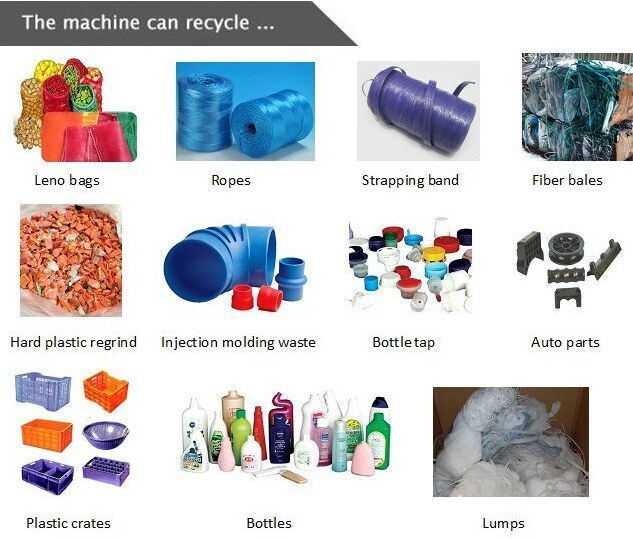
Parameters
PRODUCTS | PP/HDPE/LDPE/LLDPE/EVA/ABS/PS | |
MAX. OUTPUT /Â HR . | PP | 600KG |
HDPE | 700KG | |
LDPE | 800KG | |
INSTALLED POWER | 420KW | |
SHREDDING UNIT | DRIVING MOTOR | 110KW |
SHREDDER DRUM DIA(m/m) | 1300 | |
SHREDDING KNIVES | 9 FOR ROTARY | |
13 FOR STATIONARY | ||
EXTRUDER | SCREW DIAMETER(m/m) | Ø160mm |
L/D RATIO | 30/1 | |
SCREW RPM | 10-120 | |
BARREL HEATER | 75KW | |
BARREL COOLING | BY AIR | |
TEMPERATURE CONTROL ZONE | 0.5KW×5 |
Detailed photos
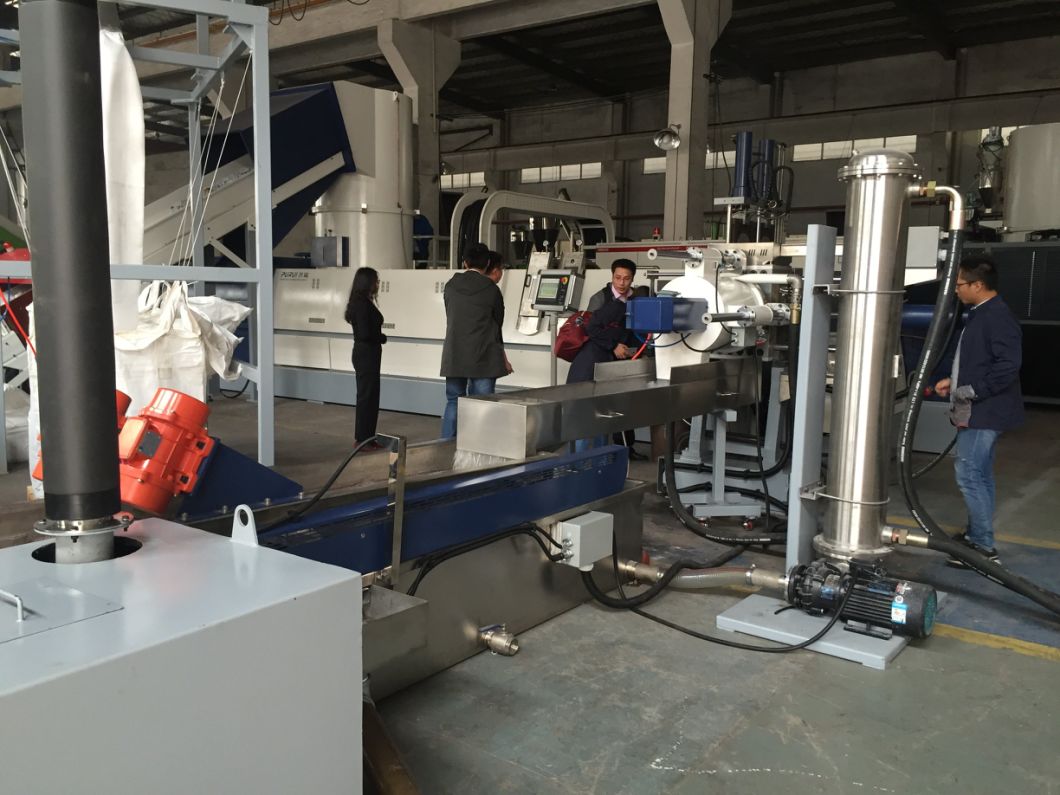
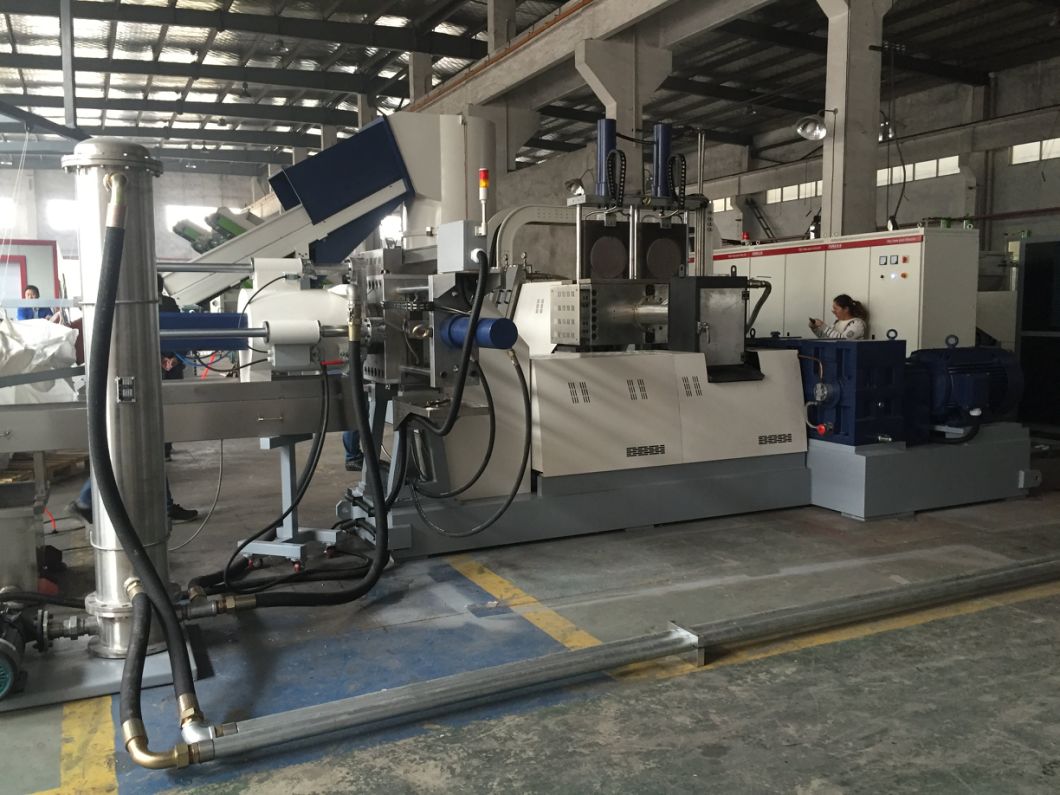
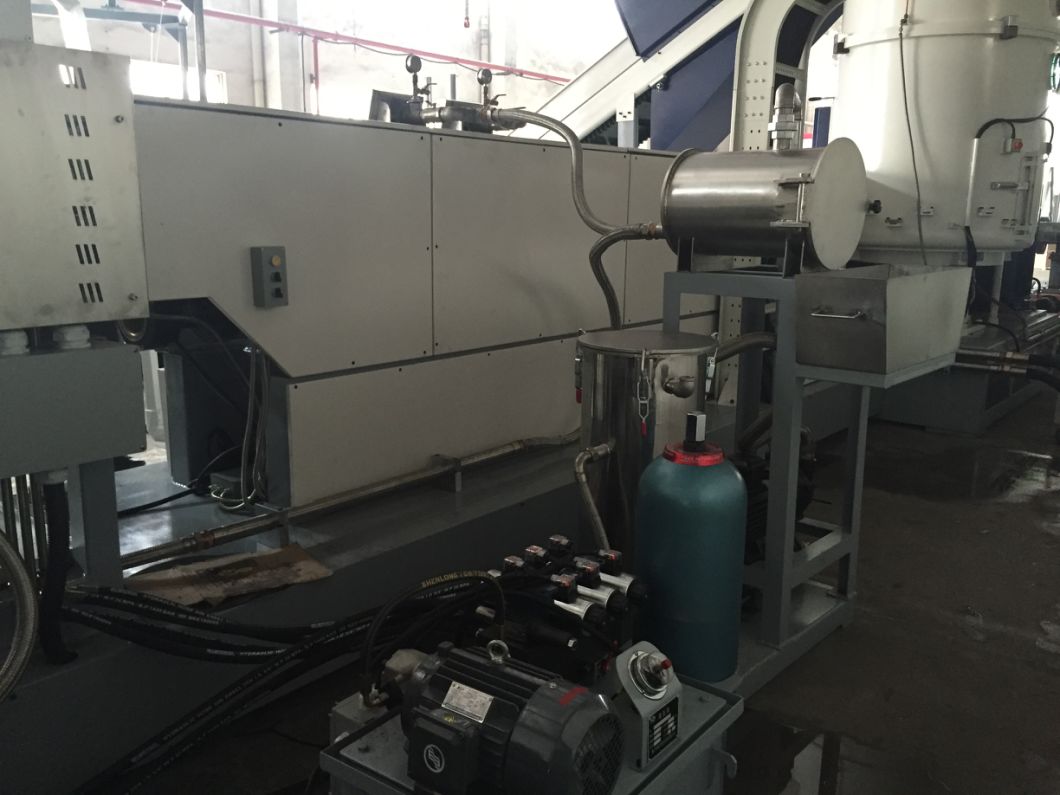
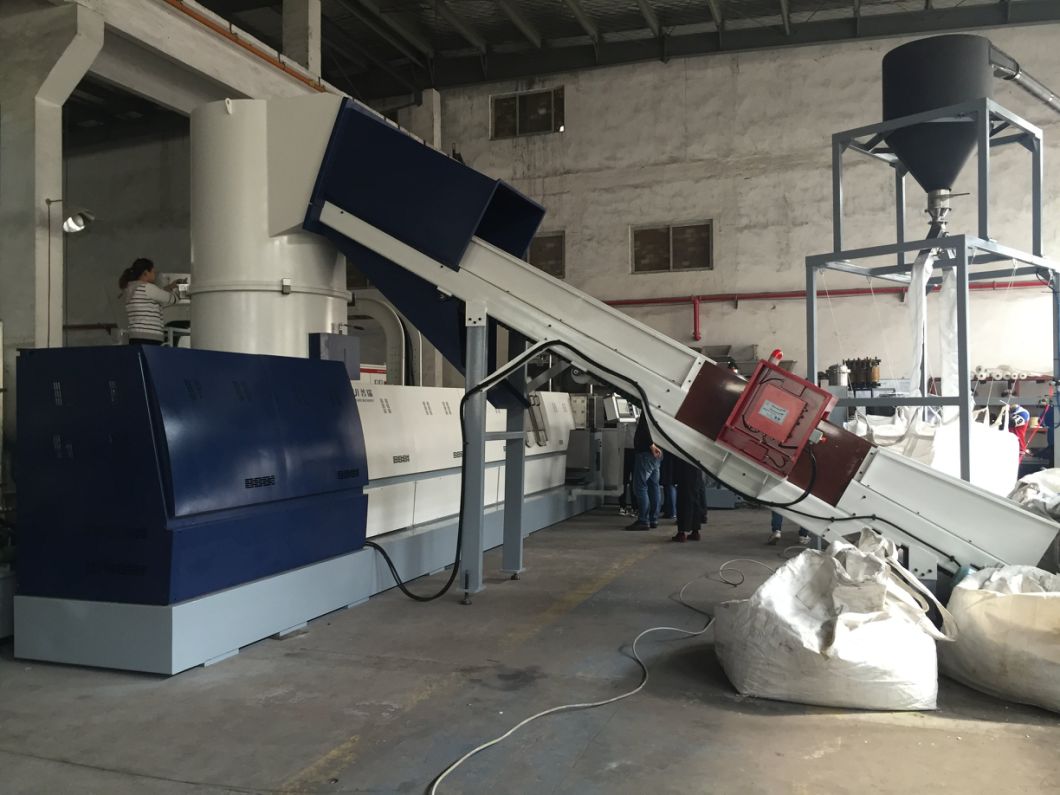
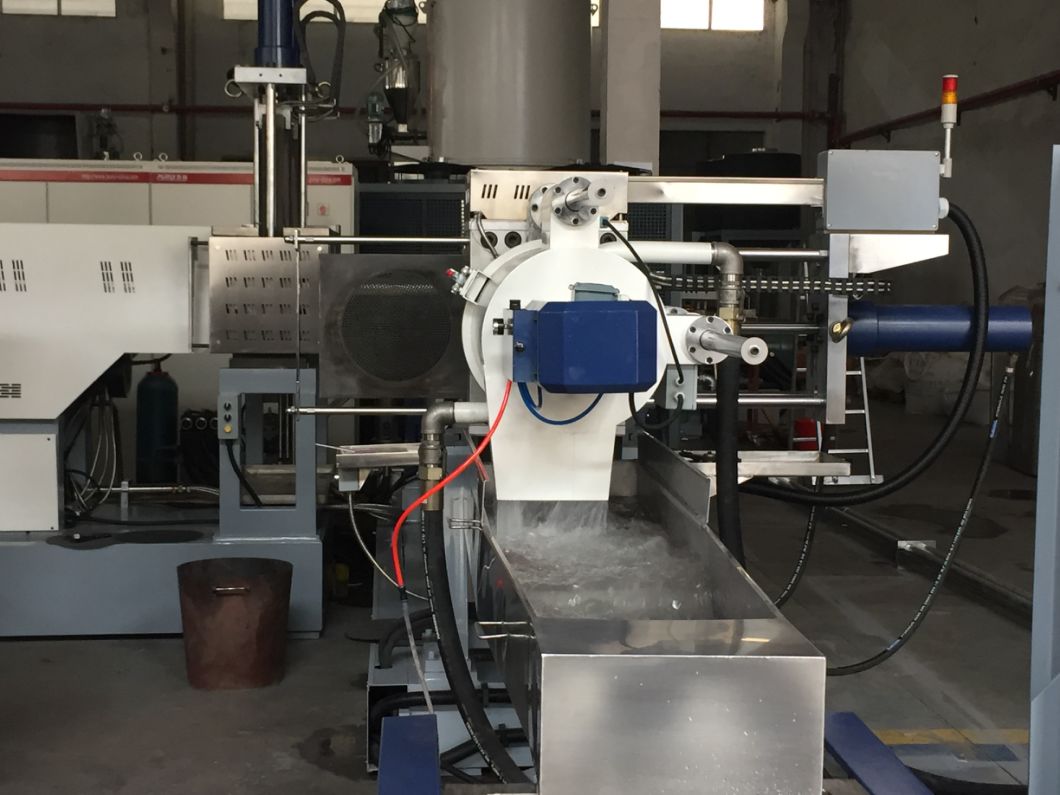
Before-sale
• Introduce products in detail  Â
• Recommend suitable solution  Â
• Offer test
During manufacturing
• Provide layout and engineering conditions  Â
• Offer screw plan and related documents
• Inform the project processing status Â
• Insure the product designed in accordance with technical document
After-sales service
• Send engineers to install, test the machines and offer technology guidance and worker training at customers' factory.
• Offer 12 months free maintenance and life long service. After the warranty period, spare parts will be provided at basic cost.
• Build customers database. All machines are traceable.
• Visit customers and make quality trace periodically and take customers' feedback into account during routine practices.
• Speed up service and spare parts supply.
Feel free to contact with me if you have any questions:
Contactor: Ms Laura
Mobile: 86 159 6236 6319Â : )